Phone: +86-755-2357-1819 Mobile: +86-185-7640-5228 Email: sales@ominipcba.com whatsapp: +8618576405228
Lead-Free PCB Assembly by Omini
Omini specializes in providing high-quality, RoHS & REACH compliant lead-free PCB assembly services. With a comprehensive range of assembly techniques and stringent testing processes, we ensure reliable and cost-effective solutions for every project.
RoHS & REACH Compliant PCB Assembly: Ensuring environmental safety and regulatory compliance for all your PCB assembly needs.
One-Stop Solution for PCBs, Components & Assembly: Omini offers complete PCB solutions, including sourcing components and final assembly, streamlining your production process.
SMT, PTH & Manual Assembly: We provide a range of assembly techniques, including Surface Mount Technology (SMT), Pin Through Hole (PTH), and manual assembly, tailored to your requirements.
ISO9001:2015 Certified & UL Listed: Omini adheres to international quality standards, ensuring reliable and safe products.
100% E-test, AOI, ICT, FCT: We perform rigorous testing, including Electrical Testing (E-test), Automated Optical Inspection (AOI), In-Circuit Testing (ICT), and Functional Testing (FCT) to ensure product quality.
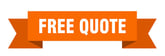
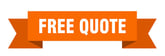
Introduction to Lead-Free PCB Assembly
Omini specializes in RoHS-compliant, lead-free PCB assembly services. Lead-free solder eliminates hazardous substances and supports environmental safety standards. Unlike leaded solder, which typically consists of 63% tin and 37% lead, lead-free solder, such as SAC305, contains 96.5% tin, 3% silver, and 0.5% copper. This transition is driven by health and environmental concerns, as lead is toxic and non-compliant with RoHS regulations. Common lead-free solder types include:
• SMT Solder Paste: 95.5% Sn / 4% Ag / 0.5% Cu or 96.5% Sn / 3.5% Ag
• Wave Solder Bar: 99.3% Sn / 0.7% Cu
• Soldering Wire: 99.3% Sn / 0.7% Cu
At Omini, we ensure all our lead-free PCB assemblies meet international safety and environmental standards for quality and compliance.
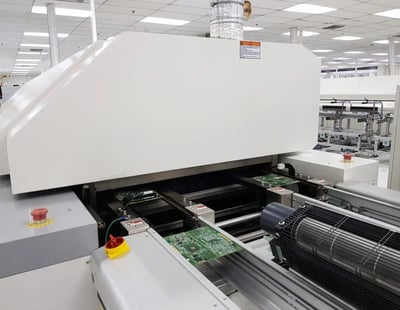
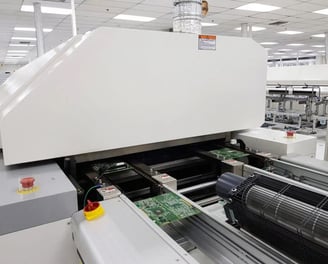
Omini: One-Stop Lead-Free PCB Assembly Manufacturer
1. 16+ Years of Industry Experience
With over 16 years of experience, Omini has established a strong reputation for its professionalism, innovation, and commitment to delivering high-quality services. Our expertise is recognized globally, making us a trusted partner in PCB assembly.
2. Skilled Production Team
At Omini, we have a highly skilled team dedicated to providing top-tier lead-free PCB assembly services. Utilizing the latest RoHS-compliant technologies, we ensure that all our PCBs meet environmental and quality standards.
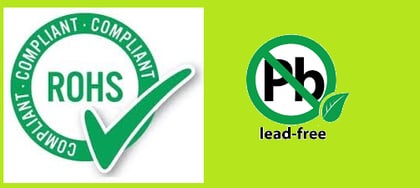
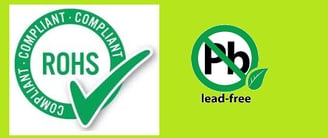
3. Excellent Customer Support
Omini offers fast, professional, and personalized customer service, ensuring smooth communication at every stage: pre-sales, in-sales, and post-sales. Our dedicated team is always ready to support and address your needs efficiently.
4. Competitive Pricing
We offer the best value for your investment, combining competitive pricing with exceptional quality and fast delivery. Omini is known for its superior products, cost-effective solutions, and reliable customer service, earning us strong customer loyalty.
When Should We Use Lead-Free PCB Assembly?
Lead-free PCB assembly is essential for RoHS-compliant electronic products and has become a global standard in the PCB assembly industry. With increasing international environmental regulations, lead-free PCB assembly is now a mandatory process in the electronics manufacturing sector.
Omini specializes in lead-free PCB assembly, ensuring compliance with RoHS standards by replacing traditional lead-based solders with safer, environmentally-friendly alternatives. While some companies continue to use leaded processes for their excellent solderability, the shift towards lead-free methods is accelerating worldwide due to environmental concerns.
You should consider lead-free PCB assembly if:
• Your products are intended for markets with regulatory requirements like the European Union.
• Your local or state government mandates lead-free manufacturing, such as in California, USA.
• Health risks from lead-based materials are a concern for your product’s safety.
• You want to reduce liability risks associated with lead-containing products.
• You’re committed to green manufacturing practices and want to maintain customer trust with eco-friendly production.
• You seek reliable, high-quality lead-free PCB assembly without compromising on mass production standards.
By choosing Omini for your lead-free PCB assembly needs, you’re opting for a trusted, environmentally-conscious partner that adheres to the highest quality and industry standards.
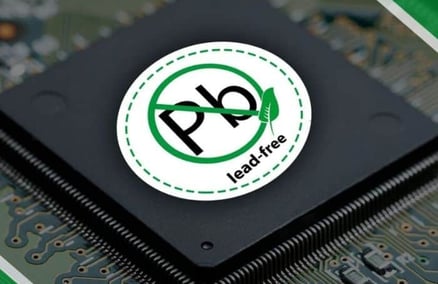
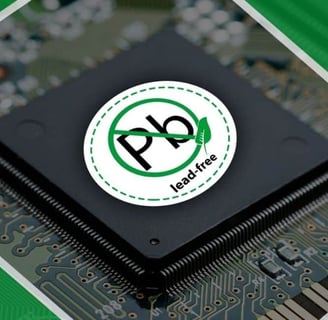
Differences Between Leaded and Lead-Free PCB Assembly
Here are the key differences between leaded and lead-free PCB assembly (RoHS-compliant):
1. Environmental Impact
The primary difference is environmental protection. Leaded solder contains lead (Pb), which is toxic and not environmentally friendly. In contrast, Omini uses lead-free solder that complies with RoHS standards, making it safer for both human health and the environment.
2. Metal Composition
Leaded solder typically contains 60% tin and 40% lead, while lead-free solder, like SAC305, is composed of 96.5% tin, 3% silver, and 0.5% copper. Although lead-free solder isn’t 100% lead-free, it contains less than 0.1% lead, which meets RoHS and REACH requirements.
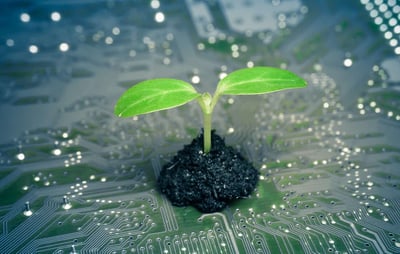
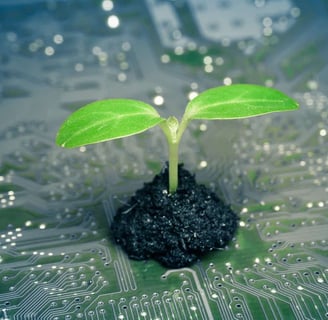
3. Soldering Temperature
Leaded solder has a melting point of 180–190°C, while lead-free solder melts at 210–230°C. The operating temperature for lead-free solder ranges from 250 to 280°C. However, low-temperature lead-free solders, which melt below 200°C, are available.
4. Cost Considerations
Lead-free solder is generally more expensive due to the higher cost of base materials. However, Omini ensures competitive pricing without compromising on quality for your lead-free PCB assembly needs.
By choosing Omini for your lead-free PCB assembly, you benefit from a reliable, environmentally-friendly solution backed by 16+ years of industry experience.
How to Distinguish Lead-Free PCB Assembly and Leaded PCB Assembly?
When receiving a PCB, it’s important to determine whether it is lead-free or leaded, especially for RoHS-compliant PCB assembly. Here’s how to distinguish between them:
1. Appearance Difference
Experienced technicians can easily tell the difference by the color of the solder joint. Leaded solder tends to appear bright white, while lead-free solder is darker with a slight yellowish tint.
2. Composition Difference
Leaded solder typically contains 70% tin and 30% lead. In contrast, lead-free solder used for Omini’s RoHS-compliant PCB assembly is composed of 96% tin, 3% silver, 0.5% copper, and trace amounts of other elements.
3. Usage Difference
Leaded solder is only used in products where lead is permitted, whereas lead-free solder, used in Omini’s lead-free PCB assembly, is RoHS and REACH compliant, making it suitable for international markets like the EU and the US.
By understanding these key differences, you can quickly identify whether a PCB is lead-free or not.
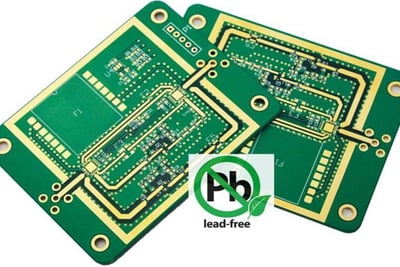
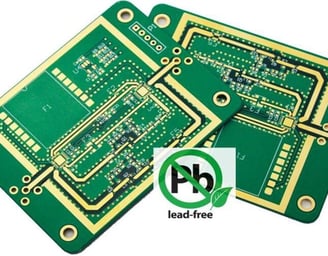
Key Factors in Lead-Free PCB Assembly
Lead-free PCB assembly is becoming increasingly common in the industry. To ensure the production of high-quality lead-free PCBs, here are key factors to consider:
1. PTH Wave Soldering Time
Accurate timing is critical during PTH assembly. The welding process should be completed in a few seconds to avoid incomplete soldering or poor contact. If the time is too long, the flux will evaporate, rendering it ineffective, while too short a duration may prevent the solder from fully melting, leading to faulty joints.
2. Amount of Solder and Flux
The correct amount of solder and flux is essential for ensuring strong, reliable joints. Too much or too little can compromise quality. It’s important not to disturb the welding area before the solder solidifies to prevent deformations or poor connections, known as cold soldering.
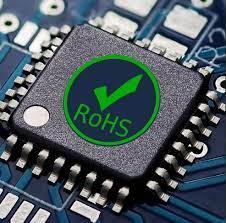
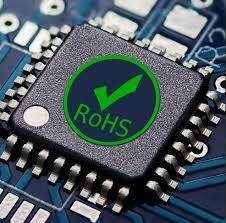
3. Temperature of the Soldering Iron
For manual soldering, maintaining the right temperature is crucial. The ideal temperature is when the flux melts without excessive smoke. This ensures that the soldering process is smooth and efficient, yielding optimal results.
4. Ensure All Materials are Lead-Free
To achieve RoHS-compliant lead-free PCB assembly, it’s essential that all components, including PCBs and electronic parts, are lead-free. Always verify with suppliers that the components meet RoHS standards.
5. Stable Personnel
Stability in your team, especially among front-line staff and key engineers, is crucial for ensuring consistent production quality. Effective communication with customers is also essential to ensure that manufacturing processes align with agreed specifications.
6. Focus on High-Quality Products
By concentrating on areas of expertise, Omini ensures consistent production of high-quality lead-free PCBs. We emphasize small to medium-volume PCB assembly services and prioritize long-term, high-quality partnerships with clients. This focus helps maintain competitive pricing while delivering superior products.
Why Does Leaded PCB Assembly Still Exist in the Industry?
Although leaded PCB assembly is harmful to both human health and the environment, it remains prevalent in the industry. However, Omini focuses exclusively on providing RoHS and REACH-compliant, lead-free PCB assembly solutions, adhering to the highest environmental standards.
1. Special Product Requirements
Some products require specific soldering standards that cannot be achieved with lead-free solder. In these cases, leaded soldering may be necessary, particularly for components that cannot withstand the higher temperatures associated with lead-free processes.
2. Cost Considerations
Leaded PCB assembly typically offers lower production costs compared to lead-free assembly. This cost advantage leads many manufacturers, especially those producing large quantities of low-cost electronic products, to continue using lead-based processes.
3. Regulatory Differences
In some regions, RoHS and REACH regulations are not yet mandatory, allowing leaded PCB assembly to remain common. However, Omini strictly adheres to these regulations, ensuring all assemblies are compliant with environmental standards.
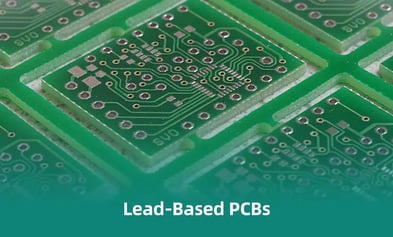
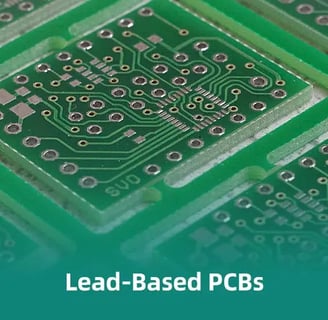
Considerations for Choosing Lead-Free PCB Assembly Services
When deciding between lead-free and leaded PCB assembly, many customers face challenges. Omini helps guide the decision-making process by considering key factors:
1. Environmental Policy, Price, and Profit
Lead-free PCB assembly is primarily driven by environmental concerns, as it reduces health risks and environmental impact. For RoHS and REACH compliance, lead-free assembly is necessary. However, lead-free solder costs more, which can increase overall assembly expenses. Customers should balance environmental requirements, cost, and product profitability before making a decision.
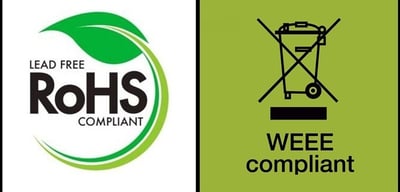
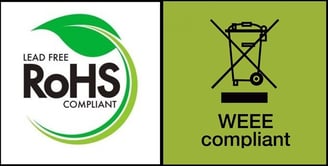
2. Lead-Free Soldering Requires Higher TG PCB Material
Lead-free soldering typically requires a higher soldering temperature (around 35°C higher than leaded solder). This can cause thermal deformation or damage to components if the PCB’s Tg (glass transition temperature) is too low. Choosing materials with a higher Tg is essential to prevent such issues.
3. Need for High-Temperature Resistant Components
The higher soldering temperature of lead-free assembly (up to 260°C) demands components that can withstand these conditions. The packaging of components, especially for BGA, CSP, and similar packages, must be able to endure higher temperatures during the soldering process.
4. Impact of High Temperatures on Internal Connections
High soldering temperatures can affect internal connections within devices, such as ICs. Advanced connection methods like gold wire ball welding and ultrasonic pressure welding are critical, especially in newer component technologies. Omini ensures that the internal connections can withstand the elevated temperatures required for lead-free assembly.
5. Cost Difference Between Lead-Free and Leaded Soldering
Lead-free solder is more expensive than traditional tin-lead solder. However, the overall impact on product cost is usually minimal, as solder typically makes up only about 10% of total production costs. For RoHS-compliant products, the higher cost of lead-free solder is a worthwhile investment for long-term compliance and environmental benefits.
Omini offers expert guidance and high-quality lead-free PCB assembly services tailored to meet both environmental standards and customer specifications.
Features of Materials Replacing Lead in PCB Assembly
As the demand for lead-free solutions grows, solder manufacturers are continuously researching the most suitable metals to replace lead while maintaining cost-effectiveness and good solderability. Here are the key features that need to be considered when selecting lead alternatives for PCB assembly.
1. Global Availability
The substitute metal or alloy must be readily available worldwide. It should be easily accessible in most countries, with a sufficient supply to meet global demand.
2. Recyclability
Alternative alloys should be recyclable to minimize environmental impact. A simple composition is preferred, as a complex mix would increase recycling difficulty and cost.
3. Non-Toxicity
Lead is toxic and harmful to both human health and the environment. Therefore, any alternative metal must be non-toxic, ensuring it aligns with environmental and safety standards.
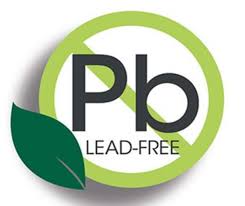
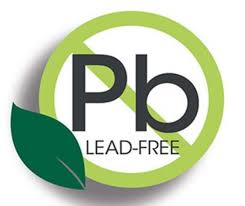
4. Industry Compatibility
The replacement material must be compatible with various PCB assembly processes, including SMT, PTH assembly, manual soldering, and repairs. It should meet the diverse requirements of the electronics industry.
Key Considerations in Lead-Free Solder Research
As the demand for eco-friendly products grows globally, more PCB manufacturers, including Omini, are shifting towards lead-free solutions to meet environmental standards. Lead-free hot air solder leveling (HASL) surface treatments are increasingly used in SMT factories to supply RoHS-compliant PCBs.
From a technical perspective, numerous countries have established lead-free solder research institutions. These institutions, alongside solder manufacturers, have developed various lead-free solder alternatives. Many of these solutions are now proven substitutes for traditional tin-lead solder. Key considerations in lead-free solder research include:
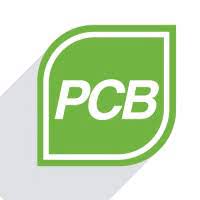
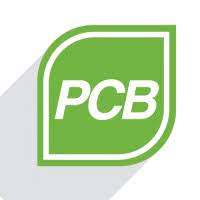
1. Non-toxic, Good Solderability, and Cost-effectiveness
A common concern is whether manufacturers will substitute lead with other harmful substances. At Omini, we ensure that lead-free solder is non-toxic and environmentally safe. Additionally, solderability and post-solder reliability remain crucial factors—ensuring that lead-free alternatives meet both environmental and performance standards, while maintaining cost-effectiveness.
2. Equipment Requirements for Lead-Free Soldering
For lead-free soldering, specialized equipment like wave and reflow soldering machines are essential. Many manufacturers are working to enhance the quality of lead-free solders to be compatible with existing equipment. Omini ensures our soldering processes are fully optimized for lead-free technology, ensuring high-quality results.
3. Compatibility with Flux and Other Materials
The latest lead-free solders must be highly compatible with various flux types. They should not only work with active rosin flux (RA) but also with milder fluxes (RMA) and resin-free cleaning flux. This versatility is essential for the continued development of lead-free soldering in PCB manufacturing, aligning with Omini’s commitment to providing top-tier, environmentally responsible assembly solutions.
Production Environment of a Lead-Free PCB Assembly Workshop
For a lead-free PCB assembly workshop, maintaining a controlled and compliant environment is critical to ensure high-quality, RoHS-compliant production:
1. RoHS Compliance: The workshop must exclusively use lead-free materials, ensuring that only RoHS-compliant PCB assemblies are processed.
2. Controlled Environment: Static electricity management, dust control, and temperature/humidity regulation are essential. Ideal conditions: Temperature 24±2°C, Humidity 60±10% RH.
3. Cleanliness & Organization: The workshop must remain free of debris, with unobstructed pathways and no water seepage. The floor should be clean and dry, with no cigarette butts or waste.
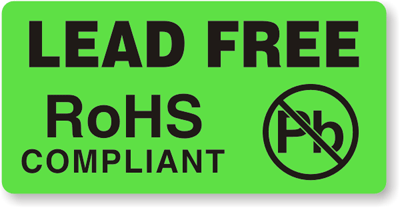
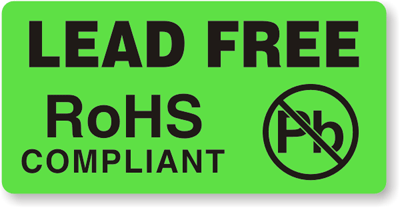
4. Ventilation & Lighting: Proper air conditioning, ventilation, and lighting are crucial. Electrical and machine layouts must adhere to safety standards, ensuring fire access is clear and fire safety equipment is available.
5. Workplace Facilities: Depending on the production needs, lockers and changing rooms should be provided and maintained clean. All tools, raw materials, and semi-finished products should be neatly organized for easy access.
6. Cleanliness Maintenance: After each shift, production teams must clean the workspace, ensuring waste is properly disposed of. Daily cleaning, particularly of floors and corners, is essential to maintain a pristine environment.
7. Safety Education: Omini places a strong emphasis on safety, providing regular safety training for all staff, especially new employees. Workshops should conduct safety and environmental training, hold safety meetings, and address employee concerns promptly.
By adhering to these guidelines, Omini ensures a safe, efficient, and environmentally friendly production process for lead-free PCB assembly.
Contacts
Email: sales@ominipcba.com
Mobile: +86-185-7640-5228
Copyright © 2007-2025. Omini Electronics Limited. All rights reserved.
Head Office: +86-755-2357-1819
Products & Services
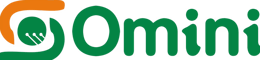
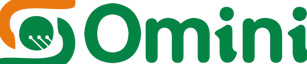
Office Address: No. 605, Tongxin Technology Building, Bao’an Avenue, Bao’an District, Shenzhen, Guangdong, China.
SMT Plant: A Building, Longwangmiao Industrial Park, Baishixia Community, Fuyong Street, Bao'an District, Shenzhen, China.
Omini Electronics Limited is an expert in trusted PCB Fabricaton and PCB Assembly in China since 2007. We have served over 1000 global customers with high-quality, low to medium-volume production. Certified by UL (E532498), ISO9001:2015, and ISO13485:2016, we offer expert electronics manufacturing services, including PCB manufacturing, assembly, and contract manufacturing, ensuring top-tier quality and precision in every project.