Phone: +86-755-2357-1819 Mobile: +86-185-7640-5228 Email: sales@ominipcba.com whatsapp: +8618576405228
Rigid Flex PCB Solutions by Omini
At Omini, we specialize in providing high-quality Rigid Flex PCB solutions. With over 16 years of experience, we offer customized manufacturing services to meet the needs of various industries, from automotive to medical devices and wearable electronics.
DuPont Pyralux® AC, AG, AP, HT, TA/TAS; Ventec ThinFlex materials for high-performance, flexible circuit designs and robust applications.
Panasonic FELIOS R-F770/R-F775, SHENGYI SF201, 202 provide superior reliability and high-frequency performance for complex, demanding PCB designs.
2-40 Layers Rigid Flex PCB with Blind and Buried Vias designed for compact, multi-layer interconnections and high-density packaging solutions.
Impedance Control, Back Drill, Vias Plugging for precise signal integrity and minimized cross-talk in high-speed electronic systems.
Balanced & Unbalanced Rigid Flex PCB Structures, ideal for space-constrained applications such as automotive, wearable devices, and consumer electronics.
Silver Film and Silver Ink EMI Shielding solutions to enhance electromagnetic compatibility and reduce interference in sensitive electronic devices.
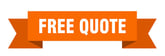
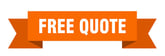
What is a Rigid-Flex PCB?
A Rigid-Flex PCB is an advanced combination of flexible circuits and traditional rigid boards. The physical structure of Rigid-Flex PCBs includes flex circuit layers sandwiched between rigid layers, creating a hybrid solution with both flexibility and mechanical stability. At Omini, we specialize in manufacturing high-quality Rigid-Flex PCBs tailored to meet the needs of a wide range of applications.
1. Rigid-Flex PCB Construction combines flexible circuits with traditional rigid boards, providing both flexibility and rigidity in one design.
2. Flex circuit layers are carefully sandwiched between rigid layers, offering high-density interconnections for compact, durable solutions.
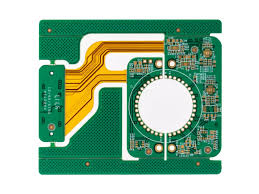
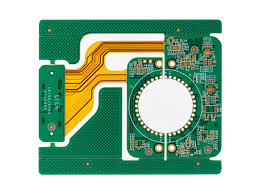
3. Prepreg Material Bonding is used, where a glass-reinforced dielectric material is cured under heat and pressure, ensuring solid mechanical integrity.
4. Rigid-Flex PCB Benefits provide the best of both worlds: flexibility for lightweight designs and rigidity for mechanical stability and reliable performance.
5. Omini designs Rigid-Flex PCBs that are ideal for demanding industries such as automotive, wearable devices, and consumer electronics, offering high performance and durability.
The Advantages of Rigid-Flex PCB Boards
Rigid-Flex PCBs offer a hybrid solution that combines the best qualities of rigid and flexible circuit designs. At Omini, we specialize in producing high-performance Rigid-Flex PCBs that offer numerous advantages for various applications.
1. Reduced Weight: The flexible portion of Rigid-Flex PCBs significantly reduces the overall weight, making them ideal for portable devices that need to be carried, worn, or held. This lightweight design enhances the performance of devices such as wearables and mobile electronics.
2. Better Flexibility: Rigid-Flex PCBs adapt well to complex and irregular shapes, fitting into tight spaces and following contours. This flexibility is measured by the material’s bend radius and the number of times it can bend without damage, which depends on the circuit design and construction.
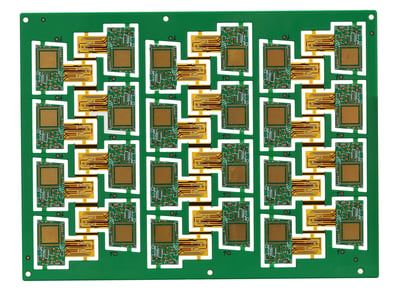
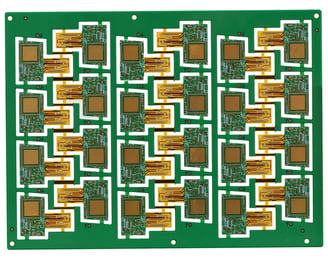
3. Smaller Device Form Factor: With Rigid-Flex PCBs, designers can eliminate bulky connectors, cables, and wires. This allows for more compact designs, making it possible to create smaller and more efficient electronic devices.
4. High Reliability: Combining the mechanical stability of rigid boards with the stress absorption capabilities of flexible circuits, Rigid-Flex PCBs provide improved interconnect reliability. These boards are built to withstand vibrations, mechanical stress, and thermal challenges, making them perfect for demanding applications in automotive, medical devices, and consumer electronics.
Applications of Rigid-Flex Circuit Boards
Rigid-Flex Circuit Boards are widely used in various industries due to their unique combination of flexibility and rigidity. At Omini, we provide high-quality Rigid-Flex PCBs designed to meet the diverse needs of cutting-edge applications.
1. Medical Products: Rigid-Flex PCBs are essential in advanced medical technologies like pacemakers and medical implants. Their compact design and low volume make them ideal for space-constrained applications in implants and wearable medical devices.
2. Military Applications: Rigid-Flex PCBs play a crucial role in military systems, where low-weight designs are critical to reducing fuel consumption in weapon systems and other military technologies. Their ability to withstand harsh environments makes them ideal for defense applications.
3. Industrial Sectors: In the industrial sector, Rigid-Flex PCBs are used in CNC machines, stepper motors, and other mechanical equipment. Their flexibility allows for better performance in rotational movements and applications requiring dynamic motion.
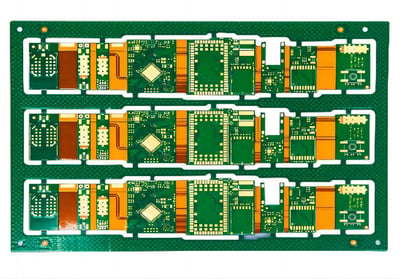
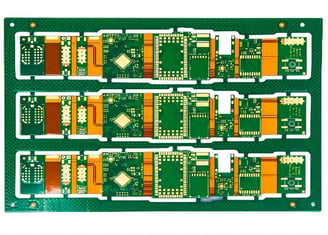
4. Consumer Electronics: Rigid-Flex PCBs are increasingly popular in consumer electronics, especially wearables like smartwatches, glasses, and ear pods. Their compact, flexible nature ensures comfort and portability, making them ideal for modern devices that require both durability and flexibility. Smartphones, media players, and game consoles also benefit from Rigid-Flex PCB designs for their compact and high-performance needs.
How Are Rigid-Flex PCB Boards Fabricated?
After the design schematics and layout are finalized, the Gerber files containing the layer stack-up information and other fabrication instructions are sent to the Rigid-Flex PCB manufacturer for production. At Omini, we ensure each step in the Rigid-Flex PCB fabrication process is executed with precision and high standards. Below is an overview of the general fabrication steps for Rigid-Flex PCBs:
1. Lamination Process: The flexible layers are laminated with the rigid sections through adhesive bonding, heat, and pressure. The flexible circuit typically consists of a polyimide core, adhesive, and copper film, while the rigid section uses an FR4 substrate, copper, and solder mask. Rigid-Flex PCB materials must be bonded precisely to meet strict specifications.
2. Drilling: Drilling is performed using either mechanical or laser drill bits based on the Gerber files, which specify hole locations. Drilling is often the slowest step, and care must be taken to minimize drill burrs. These burrs and debris are cleaned through standard methods.
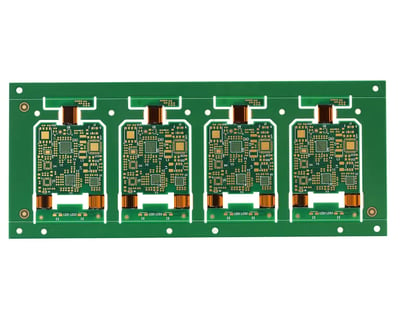

3. Copper Plating: The drilled holes, or ‘vias,’ are plated with copper to ensure electrical connections between the layers, a crucial step in creating a functioning Rigid-Flex PCB.
4. Etching: During the etching process, unnecessary copper is removed from the substrate using photolithography. A mask pattern is used to expose a photo-sensitive material, removing only the unwanted copper traces.
5. Solder Masking: The green coating on the Rigid-Flex PCB is the solder mask, which provides insulation, protection, and isolation for the conductive pads, preventing short circuits between adjacent pads.
6. Surface Finishing: To protect the copper from oxidation and to make the pads solderable, a surface finish is applied. Common techniques include Electroless Nickel Immersion Gold (ENIG), Organic Surface Protection (OSP), and Hot Air Solder Levelling (HASL).
7. Silkscreening: This process involves applying a layer of information to the Rigid-Flex PCB, such as fiducial marks, assembly instructions, and traceability details. It can be done through photolithography or direct laser printing.
8. Electrical Testing: Finally, Omini performs electrical testing to ensure the Rigid-Flex PCB meets quality standards. This includes using a Pogo pin fixture to test for continuity, ensuring only defect-free products are shipped.
Why Choose Omini as Your Rigid-Flex PCB Manufacturer?
Selecting the right Rigid-Flex PCB manufacturer is a crucial business decision. As a leading Rigid-Flex PCB manufacturer, Omini serves the global market, providing both turnkey and consigned Rigid-Flex PCB fabrication services to meet diverse customer needs.
1. High-Quality Standards: At Omini, we adhere to tightly controlled processes and written standards, ensuring that only compliant parts are shipped from our facility. Our commitment to quality is embedded in every stage of Rigid-Flex PCB fabrication, from initial planning and product design to high-volume production. Omini is ISO9001, TS13485, and UL certified, guaranteeing the highest standards of reliability and performance.
2. Competitive Pricing: As your trusted Rigid-Flex PCB supplier, we understand the importance of maximizing profitability. Omini offers highly competitive pricing by working closely with clients to establish a mutually beneficial price point that meets your budget while maintaining product quality.
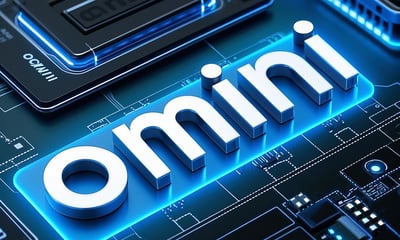
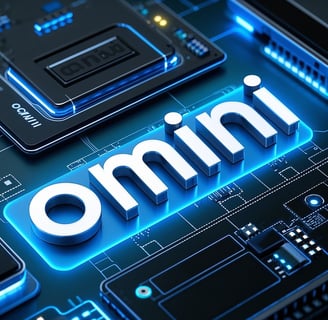
3. Reliable Products: With over 16 years of experience in the Rigid-Flex PCB industry, Omini ensures that all products undergo rigorous reliability testing before they are mass-produced. Our Rigid-Flex PCBs are designed to meet internal and external standards, ensuring that they perform within specifications and offer long-lasting product life.
4. Technical Excellence and Capability: Omini operates a state-of-the-art, high-speed manufacturing line capable of meeting your Rigid-Flex PCB needs. Our expert team, with years of experience in PCB design and fabrication, collaborates closely with customers to address any issues promptly. Whether you need assistance with Rigid-Flex PCB design or fabrication, our engineers are ready to provide solutions tailored to your specific requirements.
At Omini, we are always eager to hear your inquiries and assist you with your Rigid-Flex PCB needs. We are committed to providing the best service and support to help you succeed in your projects.
Contacts
Email: sales@ominipcba.com
Mobile: +86-185-7640-5228
Copyright © 2007-2025. Omini Electronics Limited. All rights reserved.
Head Office: +86-755-2357-1819
Products & Services
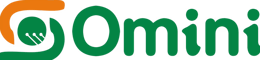
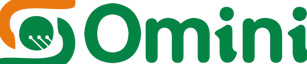
Office Address: No. 605, Tongxin Technology Building, Bao’an Avenue, Bao’an District, Shenzhen, Guangdong, China.
SMT Plant: A Building, Longwangmiao Industrial Park, Baishixia Community, Fuyong Street, Bao'an District, Shenzhen, China.
Omini Electronics Limited is an expert in trusted PCB Fabricaton and PCB Assembly in China since 2007. We have served over 1000 global customers with high-quality, low to medium-volume production. Certified by UL (E532498), ISO9001:2015, and ISO13485:2016, we offer expert electronics manufacturing services, including PCB manufacturing, assembly, and contract manufacturing, ensuring top-tier quality and precision in every project.