Phone: +86-755-2357-1819 Mobile: +86-185-7640-5228 Email: sales@ominipcba.com whatsapp: +8618576405228
What is FR4 PCB – A Complete Guide to FR4 Material and Its Applications
FR4 PCB (Epoxy Glass Fiber Copper Clad Laminate) is the core substrate of the modern electronics industry. With its UL94-V0 flame retardant certification, excellent electrical insulation and mechanical strength, it has become the first choice in consumer electronics, automotive systems, medical equipment and other fields. It is made of fiber cloth and epoxy resin, and has thermal stability (tolerance to high temperature environment), moisture resistance and corrosion resistance, and can adapt to high-frequency/high-power scenarios by adjusting the material ratio.
PCB MATERIALS
Amanda
2/5/20251 min read
Contacts
Email: sales@ominipcba.com
Mobile: +86-185-7640-5228
Copyright © 2007-2025. Omini Electronics Limited. All rights reserved.
Head Office: +86-755-2357-1819
Products & Services
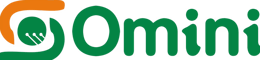
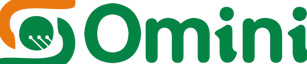
Office Address: No. 605, Tongxin Technology Building, Bao’an Avenue, Bao’an District, Shenzhen, Guangdong, China.
SMT Plant: A Building, Longwangmiao Industrial Park, Baishixia Community, Fuyong Street, Bao'an District, Shenzhen, China.
Omini Electronics Limited is an expert in trusted PCB Fabricaton and PCB Assembly in China since 2007. We have served over 1000 global customers with high-quality, low to medium-volume production. Certified by UL (E532498), ISO9001:2015, and ISO13485:2016, we offer expert electronics manufacturing services, including PCB manufacturing, assembly, and contract manufacturing, ensuring top-tier quality and precision in every project.